原価企画プロセス対策
背景
設計段階でコストの8割が決まると言われる。したがって、設計上流段階の原価企画プロセスは重要だ。しかし、出図前のコスト情報管理が設計個人管理になっていて、組織的に管理されていない企業、設計上流からのコスト削減検討結果の管理ができていない企業は依然として多い。その場合、組織的なコスト削減対策を打てず、コスト対策が後手に回り、目標未達成のまま出荷することにつながる。 本コラムでは、PLMによる試作段階からの原価企画(コスト管理)のポイントについて解説する。
試作段階からのE-BOM管理
PLMで原価企画を実現するための前提条件は、試作段階からE-BOMをPLMで管理することだ。下図は試作設計中(仕掛)⇒試作出図(試作)⇒量産出図(正式)とE-BOMが成長するプロセスを示す。例えば、図中のA1,1、P1,1、P4,1はE-BOM中の品番とリビジョンを示すが、量産出図後はそれぞれA1,2、P1,2、P4,2にリビジョンアップされている。さらに、P2,1が削除され、P5,1とP6,1が追加されている。ポイントは、設計初期段階から、量産品番を採番し、成長過程をE-BOMで管理することだ。このようにPLMの中で、E-BOMの成長過程を管理できると、同時にコストの成長過程も管理できるようになる。
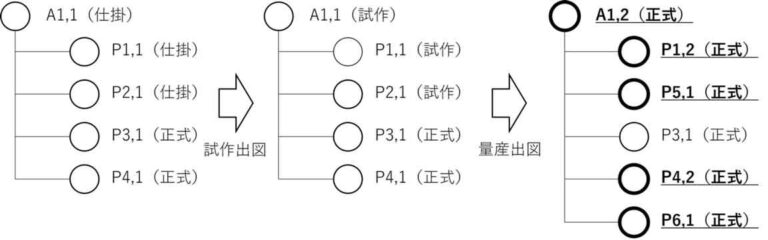
PLMによる原価企画のイメージ
下図は、試作段階からE-BOMを管理した場合の、各フェーズのコスト集計のイメージを示す。設計原価情報を、目標、見積、量産の3つの品目属性で管理する。目標は、製品から分解された部品のコスト目標値である。見積は出図された図面に基づき、調達部門がサプライヤから入手した見積情報である。実績は、量産部品の実績コストでERPからフィードバックされたものだ。 量産>見積>目標の順に精度は高いので、精度の高い値を優先使用して製品コストを逐次集計し、共有する。製品コスト目標と集計値に乖離がある場合は、即時対策を講じるのである。 まとめると、PLMで試作段階からE-BOMを管理すること、各品目が管理するコスト情報を用いて目標との乖離を逐次モニタリングし、組織的に対策を打つことがポイントである。
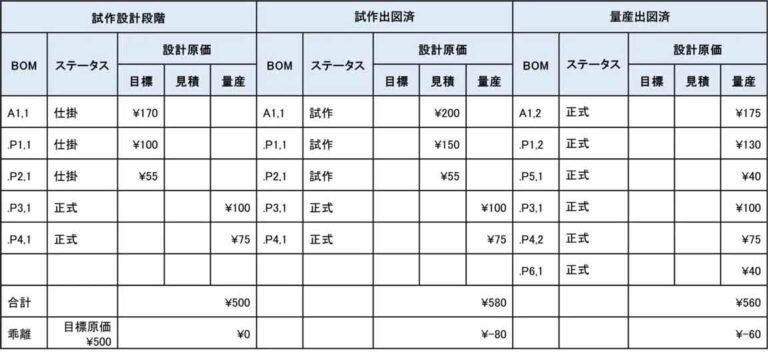